A servo system is a control device that operates according to command instructions, applied in the servo control of motors. Sensors are installed on the motor and the controlled machine, and the detection results are compared with the command values in the servo amplifier. It can be understood that servo motors are controlled by feedback signals, which differentiates them from stepper motors that rely on input pulse signals for control.
Servo motors allow for very precise control of speed and position, converting voltage
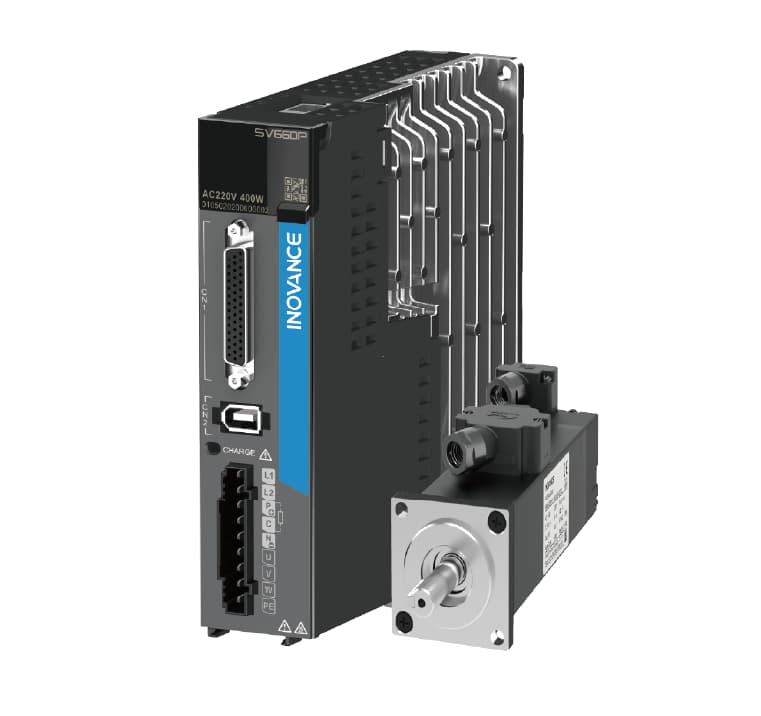
signals into torque and speed to drive the controlled object. The rotor speed of a servo motor is controlled by the input signal and can respond quickly. In automatic control systems, they serve
as actuators and possess characteristics such as small electromechanical time constants, high linearity, and starting voltage, enabling them to convert received electrical signals into angular displacement or angular velocity outputs on the motor shaft.
The key component of an absolute value servo motor is its absolute value encoder. This encoder serves as an important sensor for mechanical position angles, lengths, and speed feedback in industrial applications, playing a crucial role in the precise control of the motor.
Since 2018, the use of absolute value servo motors in stage machinery has led the development of servo motors in this field. Their characteristics of high precision, high reliability, and fast response can meet the demands of stage machinery in complex performance scenarios, such as precise control of stage lifting, sliding, and rotation, ensuring the smoothness and safety of performances.
Differences Between Absolute Value Encoders and Incremental Encoders
- Incremental Encoders:
- Working Principle: They represent changes in position through output pulse signals, requiring continuous counting by subsequent devices to determine position. This is a method of measuring relative position information.
- Advantages and Disadvantages:
- Advantages: Generally cheaper than absolute value encoders, and their performance is sufficient for applications requiring low resolution.
- Disadvantages: Requires a reset operation at each startup; otherwise, the exact position of the motor shaft cannot be determined. Errors such as missed counts and cumulative counts may occur.
- Absolute Value Encoders:
- Working Principle: They establish a reference point after device initialization, and all subsequent position information is based on the absolute position relative to this reference point. Continuous counting by subsequent devices is unnecessary, as the current position value can be read directly. This is a method of measuring absolute position information.
- Advantages and Disadvantages:
- Advantages: The exact position of the motor shaft can be known at any time without needing a reset operation. For applications requiring multiple positioning, it can improve system response speed and stability. There are no errors such as missed counts or cumulative counts.
- Disadvantages: Higher cost, especially for applications requiring high resolution, where the price is even more elevated.
The Importance of the "Absolute" Concept in Absolute Value Encoders
- Independence and Uniqueness: All position values within an absolute value encoder are "absolutely" determined within the encoder after it leaves the factory. After initializing the reference point, each position is independent and unique. Each data refresh reading, both internally and externally, does not rely on previous data readings.
- Avoiding Error Accumulation: Compared to incremental encoders, absolute value encoders do not suffer from cumulative errors due to power outages or interference. Each reading is independent and unaffected by prior readings.
- Application Scenarios:
- High Speed and Cost Efficiency: Provides absolute code values for each axis position without the need for counting, allowing for direct high-speed internal readings and external outputs. This reduces the computational burden on subsequent receiving device controllers and lowers the cost of additional input components, making it suitable for industrial robots working in multi-axis parallel operations and multi-axis synchronous control fields.
- Safety and Reliability: After power is turned on or in the event of a power failure, the current accurate position can be obtained without referencing the drive. It is unaffected by interference in complex industrial electrical environments, making it suitable for applications such as wind turbine pitch systems, port machinery synchronous positioning, lifting machinery, construction machinery (tower cranes), elevators, engineering machinery, steel metallurgy, petrochemicals, hydropower, medical equipment radar cannon rotation devices, solar tracking rotation devices, and large industrial robots in heavy industry, nuclear industry, and automotive manufacturing.
- High-Speed Bus Features: Supports standard industrial field buses such as Canopen, Profibus-DP, Profinet, Ethernet industrial Ethernet, Endat2.2, Hiperface, Biss, and dedicated high-speed data transmission protocols with CRC data safety over RS485, which incremental encoders cannot achieve.
- High Bit Resolution Features: Directly outputs digital signals without internal and external counting, unaffected by the limitations of reading "pulses" and "accumulation" in high-speed response scenarios. This enables high bit resolution, meeting the demands for high-speed precise positioning and minimal step jitter in servo motors and robots, such as accurate calculations of high-order position derivatives (motion rigidity) like acceleration and jerk, as well as precise positioning of minimal sway at the front end of robotic arms.
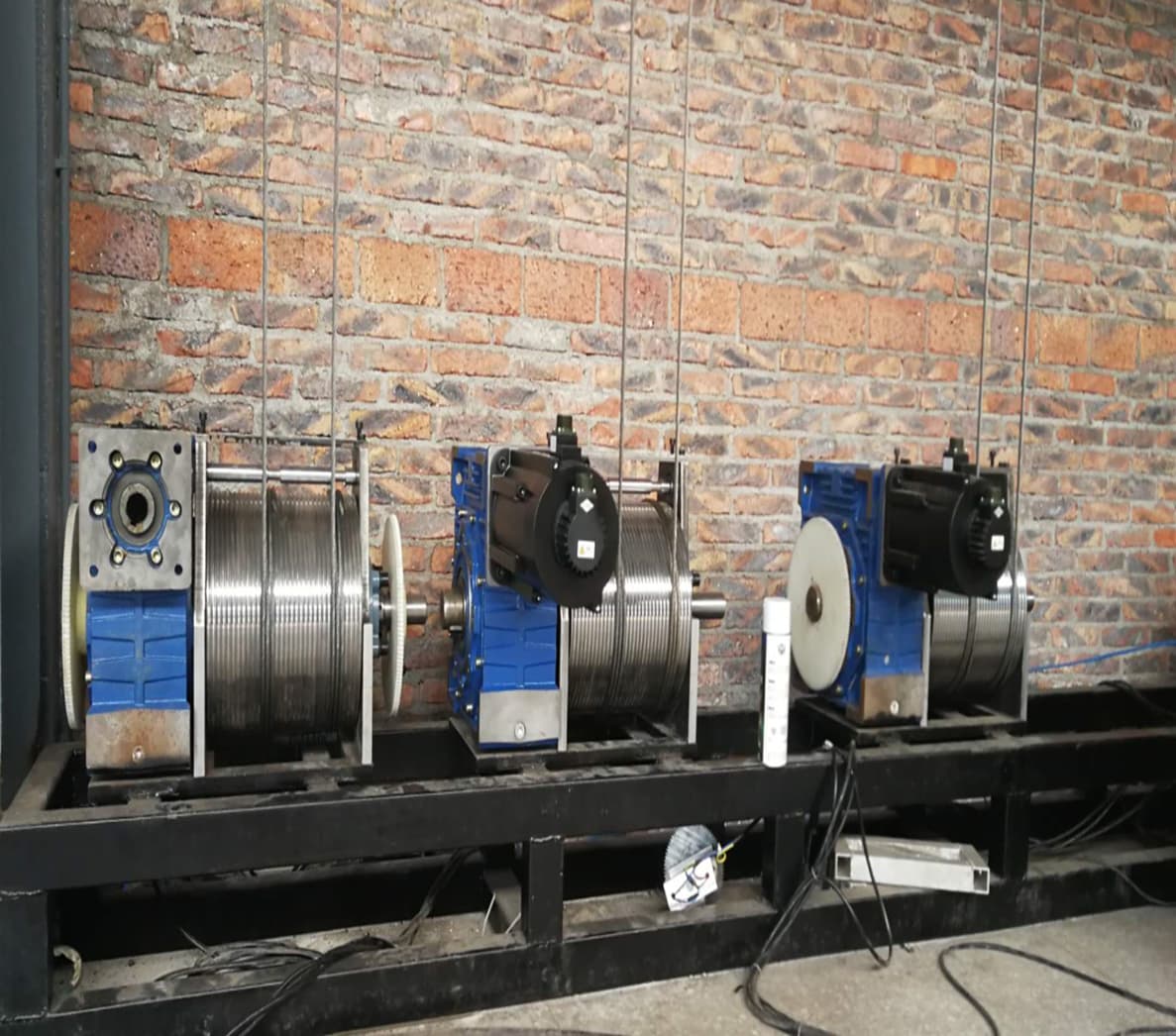
Selection and Usage Recommendations
- Avoid Confusion:
- Confusion 1: Distinguish between the "absolute working mode" of receiving devices and the "absolute" nature of absolute value encoders in servo motors. The "absolute" working mode of receiving devices can be achieved through an incremental encoder combined with its own counting and accumulation device and battery memory. However, this method carries the possibility of counting errors, accumulation errors, power supply failures of the counting device, and inability to respond at high speeds, which is different from a true absolute value encoder.
- Confusion 2: Differentiate between absolute single-turn encoders combined with internal and external counting and accumulation devices and true absolute multi-turn encoders. The former loses its "independence" and "uniqueness" after exceeding 360 degrees, relying on counting to determine the single-turn absolute position information within the total number of turns, which introduces the possibility of counting errors and power supply failures during operation. In contrast, a true absolute multi-turn encoder continues to provide "independent" and "unique" absolute coding beyond 360 degrees without relying on previous data for accumulation.
- Ensure "Absolute Coding": When selecting and using absolute value encoders, it is essential to confirm that their internal structure is indeed a true "absolute coding" system. This ensures the absolute reliability and high-speed accuracy of the data, guaranteeing that all positions are independent and unique without relying on counting (whether internal or external, with or without battery).